M2.01 Bobcat Racing Team
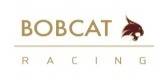
Sponsor: Ingram School of Engineering
Student Team: Jose Mendoza, Abraham Morales-Colin, Juan Rodriguez Martinez
Faculty Advisor: Dr. James Davidson
Our Team was chosen to aid in the manufacturing of components for the current 2025 FSAE racing chassis. This car participates in FSAE which is a formula style organization that competes all around the US. We are to comply with the current FSAE rules and regulations and complete our critical components.
M2.02 Non-Lethal Smart Projectile
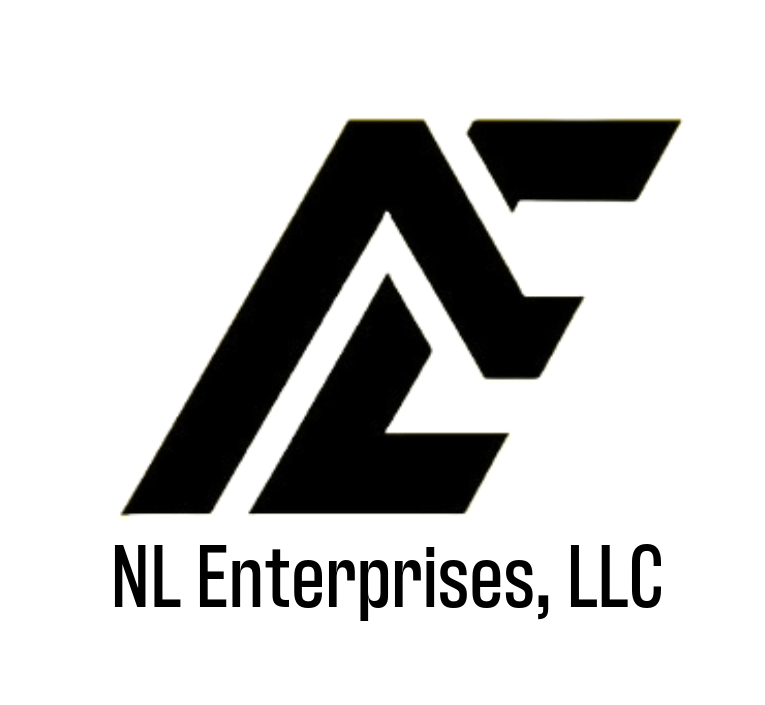
Sponsor: Non-Lethal Enterprises
Student Team: Luis Elvira-Rebollar, Wyatt Fischer & Zachary Homan
Faculty Advisor: Dr. James Davidson
There are many non-lethal projectiles used by military and law enforcement but they cannot target a small group of people or a single target without causing serious injuries or even death. These projectiles will be able to reduce the target by releasing the load in the projectile with a trigger and after traveling a desired distance or time. The Texas State manufacturing team will help manufacture a 40 mm and a .68 caliber NLE smart projectiles with the help of the Texas A&M (TAMU) electrical & computer engineering (ECE) and mechanical engineering (TAMU ME) teams as well as the Texas State (TXST) electrical engineering (EE) team.
M2.03 Improve the Lighthouse Bend EZ Punch Machine Operation
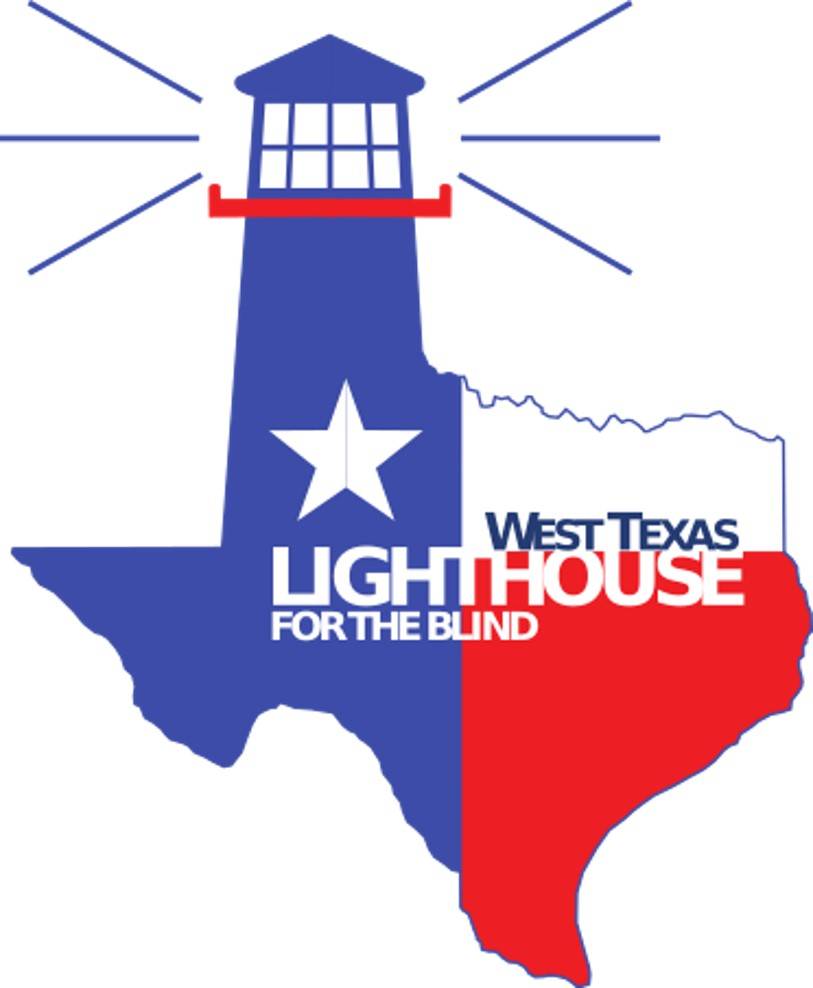
Sponsor: Ingram School of Engineering
Student Team: Holly Magee (Team Leader), Caleb Johnson, Obinna Maduagwuna
Faculty Advisor: Dr. James Davidson
Our team will be assisting the West Texas Lighthouse for the Blind, a company that provides manufacturing careers for people who are visually impaired. The employees use the current Bend EZ Cap Punching Machine, which allows them to puncture a hole in the cap of the Bend EZ pen. The current workstation raises safety concerns due to vibrations and load noises. The previous MFGE Senior Design team constructed a replica of an improved workstation for the Lighthouse. However, this workstation has a couple of concerns and does not have a Digital Twin. A digital twin is a real-time simulation of an individual product that allows for testing different solutions without financial risk and replication of the product.